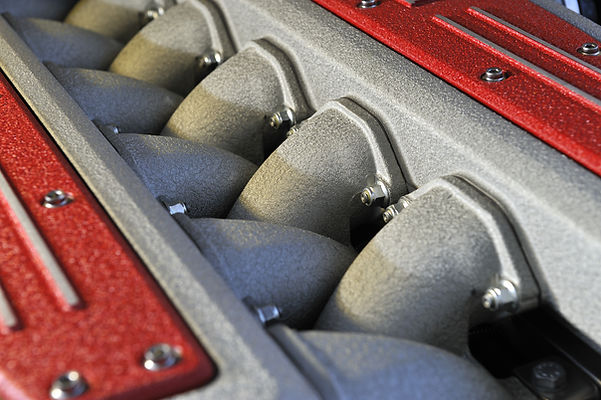
FACTS ABOUT ABRASIVE BLASTING / POWDER COATING
Pre-treatment is vital to further protect the product and improve the surface for powder coating. Abrasive blasting is the process used to clean and/or etch a surface by means of an abrasive directed at high velocity against the product or surface. The abrasive blasting facility is used to quickly remove all residual paint, surface rusts, oils, dirt or other contaminate from the metal before powder coating.
Curing
Temperature and time are essential ingredients in getting the correct finish. DIPLOCKS POWDER COATING use a computer controlled convection oven to carefully control this vital part of the process.
Size
We are not able to do a whole car, but the bullbar, side steps, roof racks can all be done separately, as well as items of furniture, bike frames, etc.
Turnaround time
Is very fast, depending on the item you want coated and the workload of our team at the time. Powder Coating is faster than painting as it is usually a one coat process.
Abrasive Blasting/Powder Coating is used by both industries and consumers. There is a long list of items that can be blasted and powder coated. Our batch oven and powder booth can coat items up to 7m x 3m x 3m.If you are interested in powder coating and would like a quote or have any questions.
Talk to the team at
DIPLOCKS POWDER COATING
on 0400 004 200 to discuss your needs
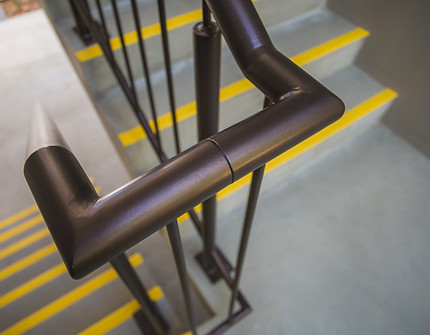
